The testing service for the chemical cleanliness of Printed Circuit Boards (PCBs)
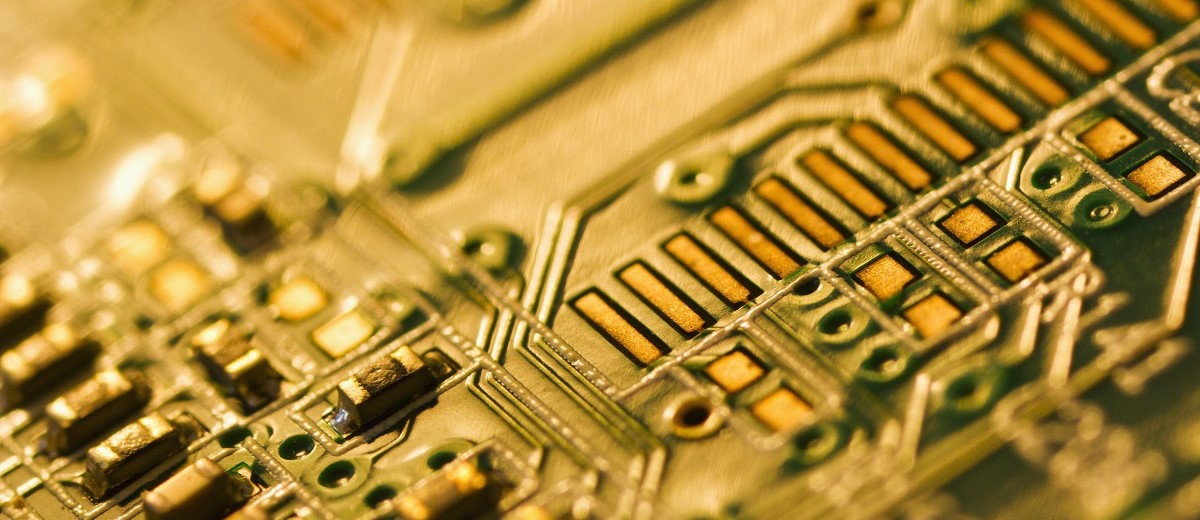
In order to ensure the quality of PCBs, the cleanliness tests of PCBs are necessary. Therefore, SGS provides a series of cleanliness testing services for ionic contamination on the surface of PCBs to assist in controlling the cleanliness of PCB products and finding the source of pollution.
IPC-TM-650 2.3.25 Rose Test
SGS provides the IPC-TM-650 2.3.25 “Resistivity of Solvent Extract (Rose) test" and selected dynamic extraction method as a process control tool that is used to inspect printed boards or printed board assemblies and determine if they conform to the monitoring level of the client’s performance specification.
Selected dynamic extraction is a high-precision method that can measure the ionizable surface contaminants in real-time and ensure the validity of test results.
Find out the source of pollution with a C3 tester
If the determined contamination level is out of the performance specification (ex. an equivalent of 1.56 µg/cm² of NaCl, the cleanliness criteria for the PCBs required in IPC-6012 section 3.9). The C3 tester can determine the contamination of a specific isolated area to find out the polluted source.
In addition, the C3 extracts a sample of the effluent from that localized region that can be used in further ionic analysis by ion chromatography.
C3 Critical Cleanliness Control
Measure the time taken to the current leakage event and determine the IPC Class level.
C3 Corrosivity Index (C.I.) test
IPC Class I (500 μA and 60 sec.) → Used on electronics for less demanding applications and environments.
IPC Class II & III (250 μA and 120 sec.) → For higher reliability electronics.
Identify and quantify the ionic contaminants on the PCB surface by Ion Chromatography.
According to the IPC-TM-650 2.3.28 or 2.3.28.2 method to analyze the ionic contamination (including anions, cations, and WOI) and inspect whether the PCBs meet the cleanliness requirements of IPC standards, such as IPC 5704.
Table 4-1 Bare Printed Board Ionic Contamination Maximum Limits (μg/cm²)
Ions |
Non-OSP |
OSP |
---|---|---|
Chloride(Clˉ) |
0.75 |
0.75 |
Bromide(Brˉ) |
1.0 |
1.0 |
Sodium(Na⁺)+Potassium(K⁺) |
2.0 |
4.0 |
Total Inorganic |
3.8 |
5.9 |
The units in Table 4-1 are in micrograms(μg) of the ion per square centimeter(cm²) based on the extraction volume and the calculated sample surface area.
Table 4-2 Inorganic lons
Cations |
Anions |
---|---|
Sodium(Na⁺) |
Fluoride(Fˉ) |
Potassium(K⁺) |
Chloride(Clˉ) |
Lithium(Li⁺) |
Bromide(Brˉ) |
Ammonium(NH₄⁺) |
Nitrate(NO3ˉ) |
Magnesium(Mg²⁺) |
Nitrite(NO2ˉ) |
Calcium(Ca²⁺) |
Sulfate(SO₄²ˉ) |
Phosphate(PO₄³ˉ) |